In wind turbine maintenance, the health of gearboxes is crucial to ensure efficient and long-lasting operation. A commonly used method to assess the condition of gearboxes is analyzing oil samples for wear debris. However, recent research has shown that optical particle counting and elemental tests performed on oil samples do not provide clear insights into gearbox health. But why does this happen?
When relying on wear debris data to make critical decisions about the maintenance of wind turbine gearboxes, it is crucial that these oil samples offer an accurate representation of the amount of debris being generated. If a gearbox is faulty and generating wear debris, you would expect it to appear in oil samples. However, data has shown that this is not the case. If the debris is not found in the sample, then where is it? There are three main reasons why oil debris is not captured in the samples taken:
1. Oil Filtration Systems
One clear answer to where the wear debris is going is simple: it has been filtered out. Filtration systems generally remove larger particles, typically between 5 and 50 µm. Therefore, most of the wear debris that is useful to assess gearbox health is filtered out before the sample is taken and analyzed. This means that oil samples may not contain the crucial wear data needed to accurately evaluate the equipment’s condition.
2. Small Sample Size
Even if the oil sample is taken before filtration, it is extremely unlikely that a representative sample of wear debris is captured in a 4-ounce beaker. Studies have shown that the average particle size distribution of wear debris in a typical fleet of wind turbines and online monitoring found that the concentration of the most abundant particles (100–200 µm) is only found once in every 20 liters of oil. Given the typical 4-ounce sample size, this means there is roughly a 0.6% chance that the sample contains any significant wear debris.
3. Irregularity of Wear Generation
Another major issue is that the generation of metallic wear debris is not a continuous or predictable process. The generation rates vary drastically depending on the fault development and operating conditions, such as temperature and wind speed. At any given time, various gearbox conditions can lead to wear debris being released, getting stuck, or settling, making it nearly impossible to collect a sample that reflects the asset’s true health at any given point.
Los sistemas de filtración eliminan la mayoría de las partículas de desgaste antes de tomar la muestra.
Limitations and Solutions
Given these factors, a small sample taken at a single point in a very complex system is not going to provide accurate or reliable results that can identify faults or make critical decisions based on gearbox health. Some samples may show debris levels that trigger warnings or alarms, while others may show nothing significant—even when a fault is present.
Online oil health monitoring can mitigate some of these risks and provide much more reliable data regarding the actual health of an asset at any given time. Poseidon Systems’ Trident DM sensors utilize real-time, condition-based monitoring to provide more accurate data on wear debris generation over time. This approach offers a more comprehensive and accurate view of gearbox health, enabling more informed and effective maintenance decisions.
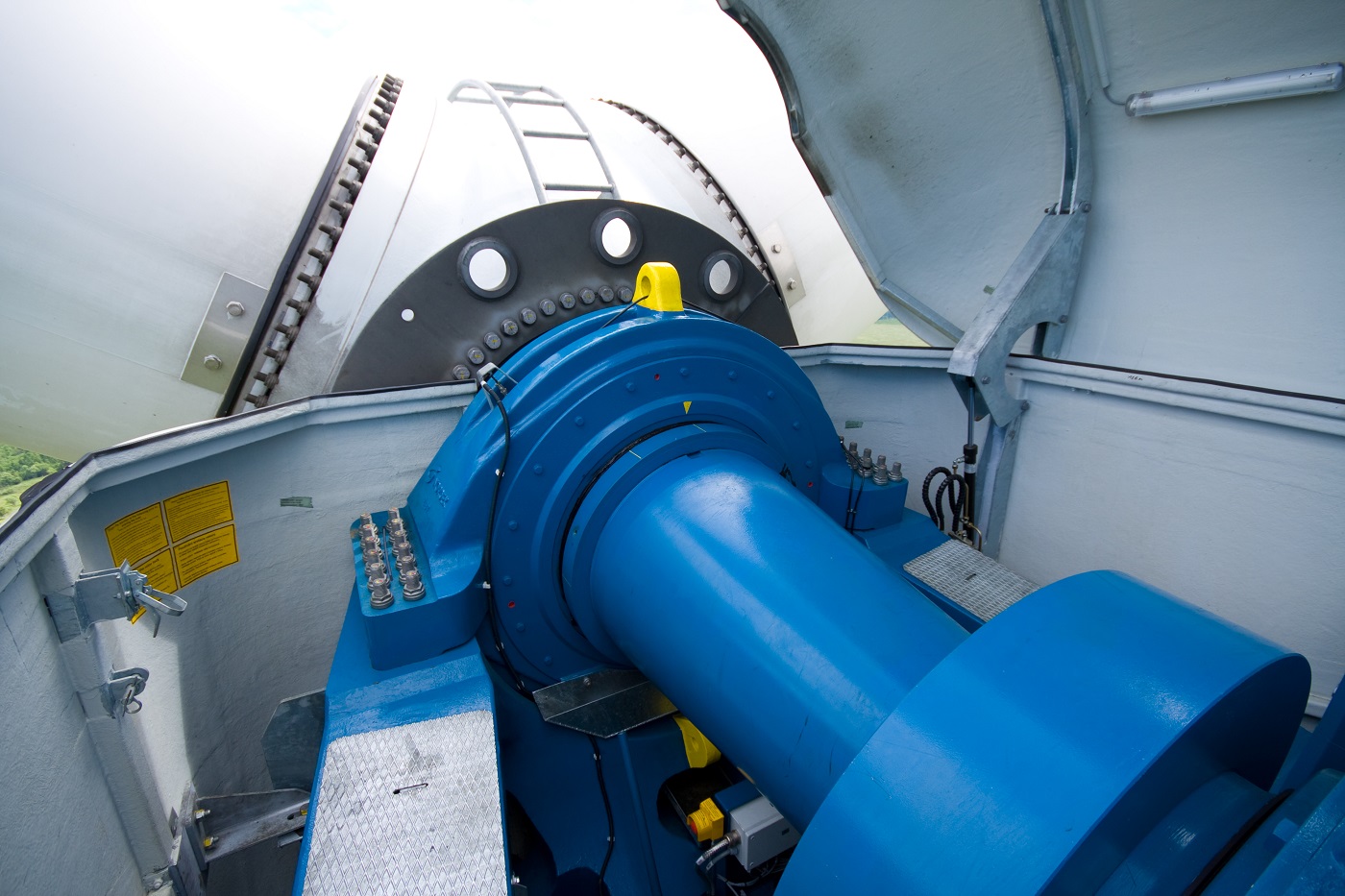